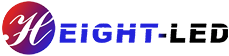
Ultraviolet light-curable inks, also known as UV inks, are currently more and more widely used in the printing industry, occupying an important position in lithographic printing, letterpress printing, screen printing and other fields. The main factors affecting UV ink curing adequacy and optimal curing speed are as follows:
1. External conditions
1) The higher the temperature, the better the curability. Therefore, in order to obtain the curing effect of the ink with strong curability and good adhesion, preheating is usually carried out. The UVLED curing lamp can be turned on and off immediately without preheating.
2) Curing environmental conditions
When printing, the room temperature should be kept as constant as possible, generally 18-25 degrees Celsius is appropriate; oxygen can hinder the polymerization of the active prepolymer, so the oxygen concentration in the light curing reaction is required to be between 3010-6 and 5010-6.
3) Light curing initiator
Adding an appropriate amount of light and curing initiator is an effective way to improve the curing effect. However, excessive addition will hinder curing, and the addition amount is usually within 4%.
4) The radiation intensity of the light source
UV light source radiation is light in one wavelength band, and the energy distribution of each wavelength is different, and the spectral sensitivity range of the UV lamp must match the UV ink; generally, the wavelength range of the UV lamp is required to be between 180~420nm, which is sensitive The area is between 350 and 420 nm.
2. Internal conditions
1) The nature of the pigment
For colored UV inks, the absorption capacity of various pigments for UV light quantum should be considered first in the arrangement of the printing color sequence. For UV photons, the transmittance of magenta is 50%~60%, and the transmittance of yellow is 20%~30%. , Cyan is 8%~20%, and black is 12%, so the order of curing rate for UV radiation is magenta-yellow-cyan-black, among which black is the slowest, so the overprint sequence during printing is black-cyan-yellow -Magenta is most suitable.
2) Ink layer thickness
The thinner the ink layer, the better the curing performance, the general colored ink layer can be fully cured in the film thickness range of 10~12nm.
3) Surface properties of printing materials
The adhesion effect of the ink depends on the wetting ability of the ink on the substrate and the force between the ink molecules. Surface treatment of the substrate is extremely important for the adhesion of UV ink. Usually, the surface tension of the ink must be less than the critical surface tension of the substrate to make the ink adhere to the surface of the substrate.
Shenzhen Height-LED specializes in the production of uvled curing equipment, and can customize suitable uvled curing systems for customers. Welcome to consult.