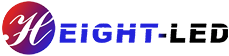
Flexible packaging printing is a graspable life-saving straw in the hands of non-adhesive label processors. It can help processors to broaden the product line, stand out in the competition of short sheet and small package, use combination and mixed printing technology, and cooperate with post-processing technology such as wiring film coating, cold ironing, value-added, etc. to expand the range of printing products, improve printing quality, and diversify production.
In the modern packaging world, more and more demanding brand holders are tending to be short edition, changeable design and fast turnover. In addition, today we see a marked increase in the use of thin films and synthetic materials to replace higher-cost cardboard and plastic bottle packaging. This means a challenge to existing packaging suppliers: to be able to provide brand holders with cost advantages of soft packaging products, but also to meet their uncompromising printing quality requirements. Based on this idea, the full-wheel UV-LED sleeve offset press just upholds the advantages of low cost offset printing. It adopts new technologies such as UV-LED drying, nitrogen flushing protection and sleeve printing drum system to realize magic-like operation conversion, which makes the traditional printing method incompetent for short-form flexible packaging work profitable.
The newly developed low ozone UV LED offset printing ink contains the least amount of light curing agent, which usually produces ozone. The newly developed nitrogen flushing protection technology greatly reduces ozone generation and protects the ink surface, although the ink contains very few light curing agents. Wide printing range can be applied to film without base paper and very thin label materials. There are also high-quality printing quality, high efficiency and rapid plate replacement, more environmentally friendly, plate cost is lower, more suitable for short and medium-term printing market demand.